SAFFS: Sustainable acrylic fabrics from seaweed
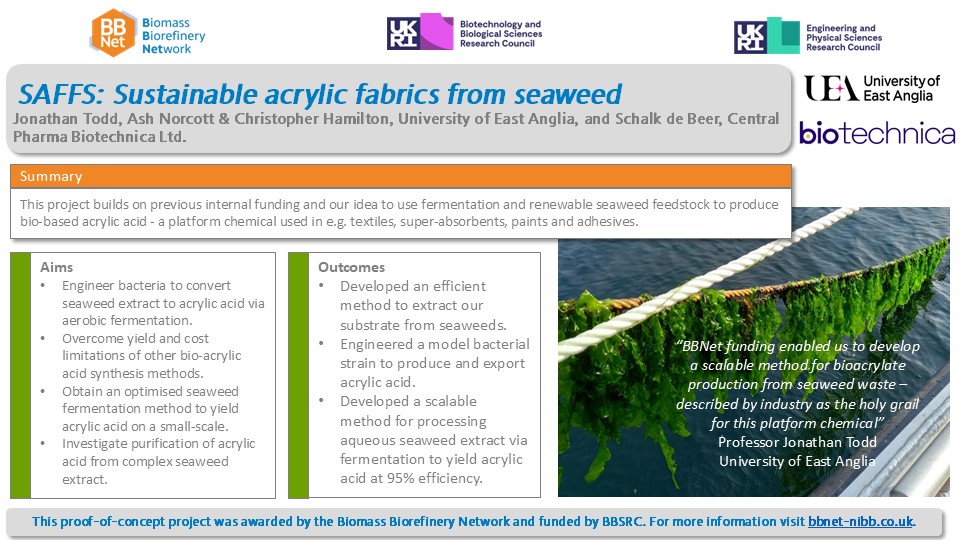
- Project lead
- Jonathan Todd
- Institute
- University of East Anglia
Summary:
Acrylic acid is one of the most mass-produced chemicals in the world and it is used to manufacture a wide range of products including textiles, superabsorbents, paints and adhesives. Currently it can only be manufactured from fossil fuels. Global concern over greenhouse gas emissions has encouraged policy makers and industry to consider bio-based chemical production. However, current bio-production alternatives are either prohibitively costly or inefficient for industrial scale.
The team’s novel methodology uses seaweed waste to create acrylic acid. This reduces processing costs and product carbon emissions. The proprietary process avoids the limitations of the current generation of bio-based chemicals. It also offers greater efficiency and the opportunity to scale to meet industrial demand.
Aims:
Sustainable acrylic acids from seaweed (SAFFS) are an alternative route to bio-produce acrylic acid, utilising bacteria and enzymes discovered in the Todd laboratory. Our engineered bacteria can convert seaweed extract to acrylic acid in an aerobic fermentation, overcoming yield and cost limitations of other bio-acrylic acid synthesis methods. The aim of this PoC project was to obtain an optimised incubation method for efficient acrylic acid production in a small-scale fermenter, and optimised purification of acrylic acid from culture broth.
Outcomes:
We have optimised small scale fermenter conditions and determined the maximum yield of acrylic acid from seaweed extract using Gas Chromatography and Nuclear Magnetic Resonance (NMR). We have analysed the composition of the culture broth with NMR and have purified acrylic acid from culture broth, achieving >60% purity.
Impact:
The impact of this work is development of an optimal small-scale method of fermentation of seaweed extract to acrylic acid for maximum yield. We are now ready to upscale this process to a larger fermenter and move into technology development with an industrial partner.
Academic partners: Prof. Jonathan Todd, The University of East Anglia
Industrial partners: Dr. Christopher Hamilton, Caledonian Seaweeds (The University of East Anglia)